Is Fraunhofer technology the solution for urban waste treatment and decarbonization?!
A revolutionary technology is generating hydrogen, synthetic fuels and biofertilizers from biomass derived from any type of waste. Developed by Fraunhofer UMSICHT, TCR® (Thermocatalytic Reforming) converts biomass into 3 by-products (coal, oil and syngas) in a two-stage process consisting of intermediate pyrolysis and catalytic reforming. These by-products are the start for the next generation of synthetic fuels or base materials for the chemical industry. TCR® can be used to convert a wide range of biogenic waste and residual materials into storable energy sources.
TCR® offers innovative solutions for biomass treatment
TCR® can be used to convert a wide range of biogenic waste and residual materials into storable energy sources. Currently, liquid energy sources and raw materials of fossil origin still account for approximately 98% of motive energy in transportation and 22% of heating energy in Germany. In addition, 16% of mineral oil is consumed in the chemical industry.
Various sectors of the economy will continue to rely on liquid energy sources with a high energy density or on mineral oil-equivalent raw materials in the future, including air traffic, shipping, heavy road transport and the chemical industry. As TCR® generates CO2-neutral energy sources from biogenic waste and can process CO2-neutral oil into standard-compliant fuels, it is a clean and safe technology for these sectors to move away from dependence on fossil fuels.
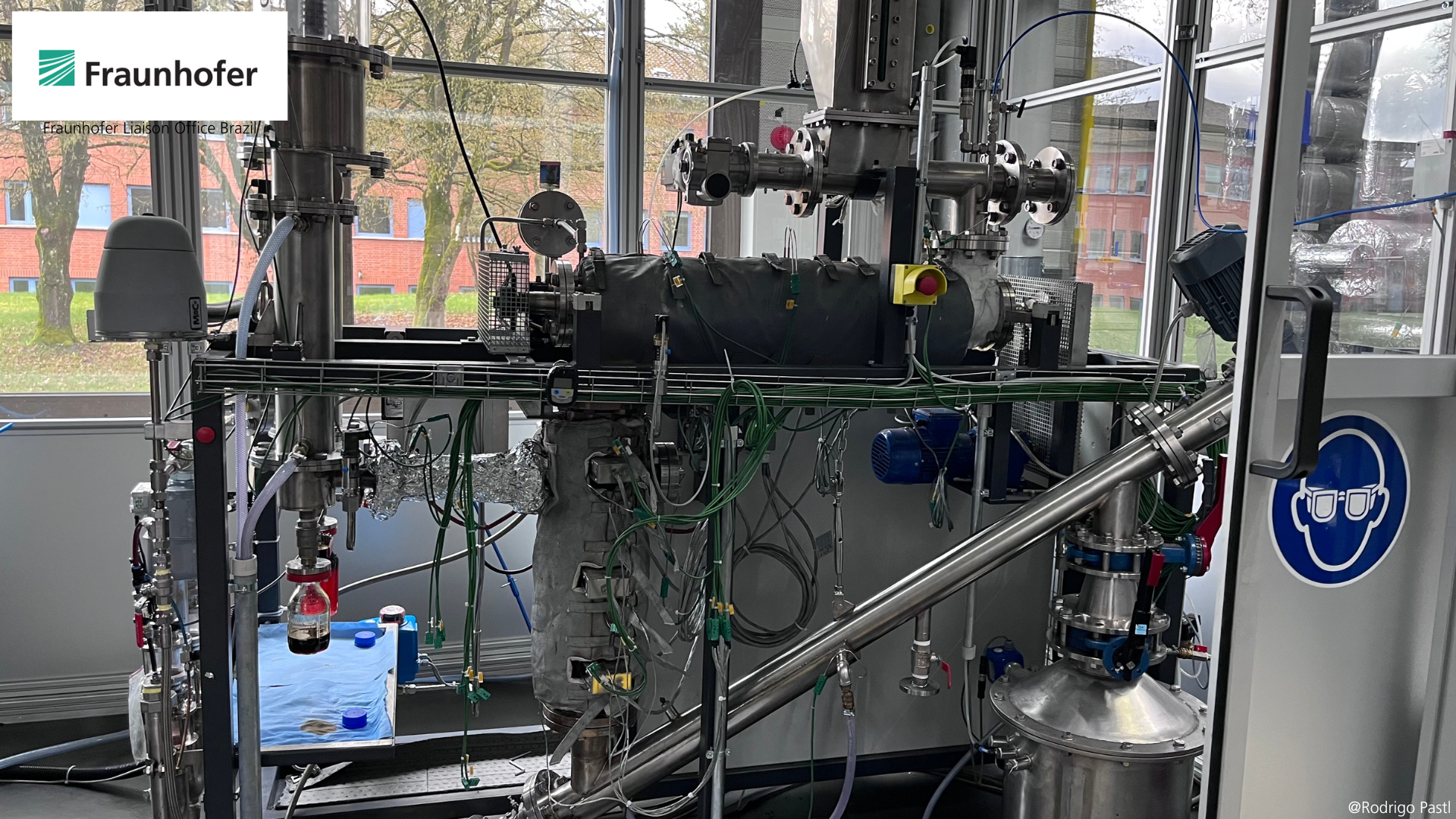
Although a promising technology, there are always points to be improved and optimized. Combustion, gasification and biomass conversion generally have to deal with restrictions related to the variety of possible input materials, compliance with emission standards and overall energy efficiency. The quality of the products obtained from biogenic waste has also not been satisfactory to date. In this context, the Fraunhofer UMSICHT institute in Sulzbach-Rosenberg has developed a new process for using biomass waste within the framework of the Center for Energy Storage, which was funded by the Bavarian Ministry of Economic Affairs at the Fraunhofer sites in Sulzbach-Rosenberg and Straubing with more than 16 million euros: thermocatalytic reforming.
In addition, the same institute built a TCR® pilot plant at the RWE Innovation Center in mid-2022 and put it into operation in the spring of 2023. In this plant, which can convert 30 kg of raw material per hour, dry sewage sludge in particular, but also other biomass, is converted. Special attention is paid to researching the liquid and solid products. They are characterized in detail and their possible uses are evaluated. Although the oil-containing liquid fraction can be processed into fuel, it is possible to use the coal as a raw material for other high-temperature conversion processes, for example in the nearby MFC (microbial fuel cells) high-temperature conversion plant.
How does TCR® technology work?
The process converts the biogenic raw material into oil, synthesis gas and coal. In a first stage, the biomass is gently broken down into biochar and volatile components in a continuously operating screw reactor in the absence of oxygen at medium temperatures (< 500 °Celsius). The formation of tar and other pollutants is prevented by optimized process conditions in the various zones of the reactor.
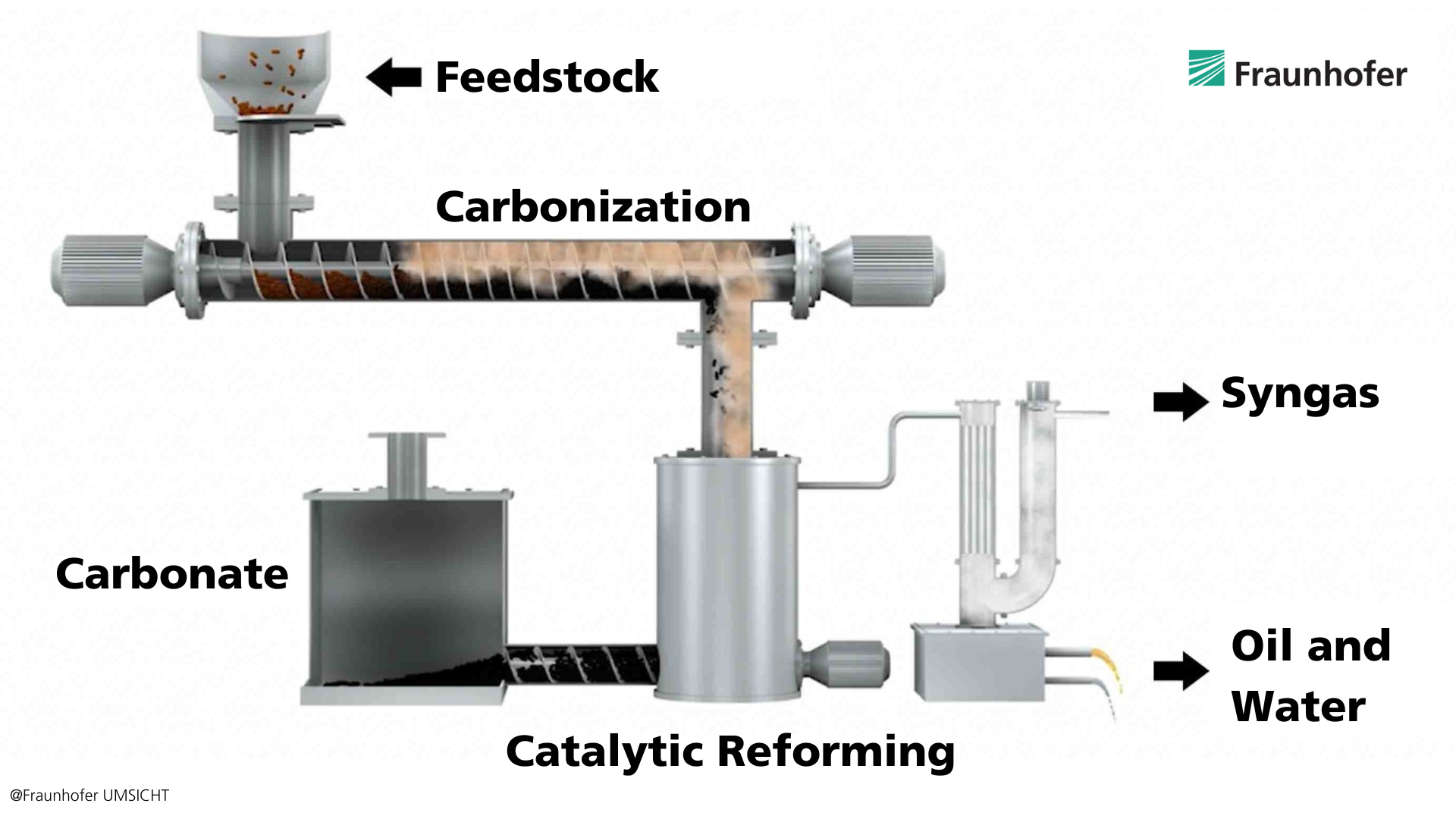
In the second stage, in a post-reformer, the coal and vapors are catalytically refined at temperatures of up to 700 °Celsius to improve gas yield and product quality. The vapors are then cooled. During condensation, the oil and process water are separated. The remaining gas is cleaned.
In the end, there are 3 by-products of the process:
- Synthesis Gas, a dust-free gaseous by-product with a very high hydrogen content of up to 50%.
- Charcoal ("biochar") with a high carbon content, which is used in-situ as a catalyst in the TCR® process itself, and can be used as a soil conditioner or stored.
- A pyrolysis oil with a consistency similar to petroleum, with a high calorific value and very low acidity values (comparable to vegetable oils). It can be refined together with mineral crude oil in refineries (co-processing) or processed into products such as gasoline and diesel.
In short, the resulting products are climate neutral. The energy required is generated from the waste used, so there are practically no CO2 emissions in the process. The input materials themselves, by definition, have no "CO2 backpack" (unlike biomass, which also has a small proportion of CO2 emissions due to cultivation).
This charcoal can be introduced into soils, as long as the raw material is not contaminated. The carbon contained in the coal is then permanently removed from the atmosphere. (Coal from the TCR process is extremely stable due to its low oxygen and hydrogen content and is not decomposed in the soil). If the carbon is sequestered in this way, the products, i.e. the oil and gas, will have a negative CO2 balance.
In the case of fuel production, the hydrogen required from the raw material is also supplied by the synthesis gas. This means that the fuels produced by the TCR process also have an almost neutral CO2 balance.
Benefits of TCR® technology
TCR® technology stands out from other pyrolysis processes due to its high energy efficiency, a wide range of input materials and, above all, the high quality of the product.
The heat needed to operate the plant is generated from residual biomass. Alternatively, surplus electricity can be used for this purpose. The gas can be used on site in a combined heat and power plant to generate electricity and heat or for fuel synthesis. Oil can be used in the mix as a storable fuel. Coal can be gasified or used to improve the soil.
In addition, there is a range of applications for waste materials. TCR® works with a broad spectrum of biomass and waste with a dry content of 70% or more, for example sewage sludge, fermentation residues from biogas plants, wood waste, landscape conservation material, industrial biomass waste such as spent grain or paper recycling sludge, biological waste fractions, straw and other agricultural waste right up to animal excrement.
Robust process with high energy efficiency
The process guarantees high operational stability, avoiding the formation of dust and tar, and can process raw materials with moisture levels of up to 30%. At the same time, it provides heat for pre-drying biomass with a moisture content of over 50%. Around 75% of the energy from the calorific value of the raw material is used in the products. If the heat provided for drying the biomass is taken into account, around 90% of the energy used will be available for sustainable use. The containerized plant design allows decentralized plant sizes to be realized economically from 300 kWel.
Large-scale plant
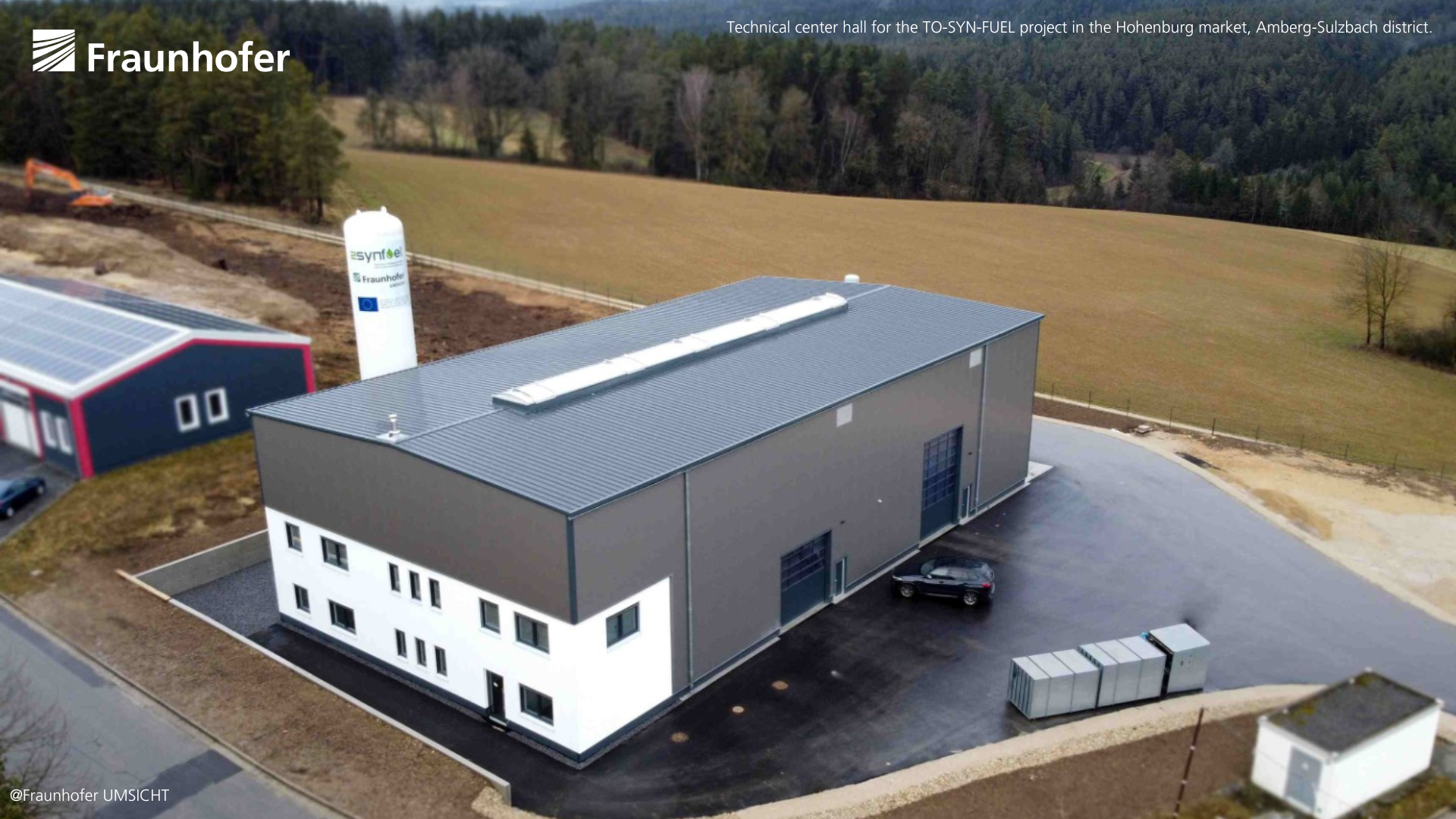
There are currently several TCR® pilot plants of different sizes: in Chile, Switzerland, Italy and Canada, there are plants capable of processing two kilos of sewage sludge per hour. 30 kilos per hour are processed in Birmingham, Sulzbach-Rosenberg and, in the future, Edmonton.
In Hohenburg (Amberg-Sulzbach district), a large-scale demonstration plant with a capacity of 500 kilograms per hour was built as part of the European Union's "TO-SYN-FUEL" project. It processes dried sewage sludge as a raw material.
Text and adaptation:
Dr.-Ing. Rodrigo Pastl